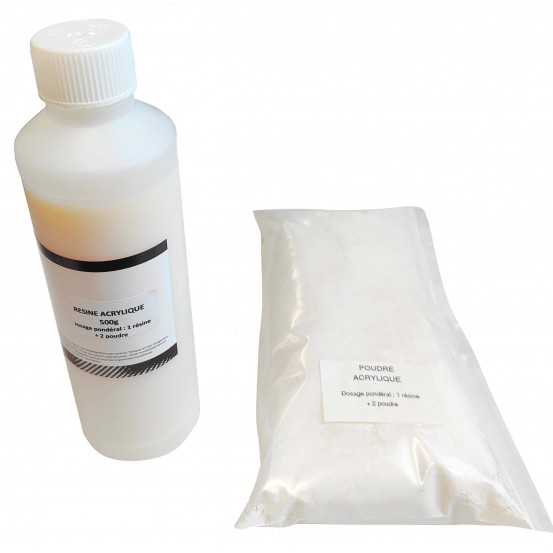
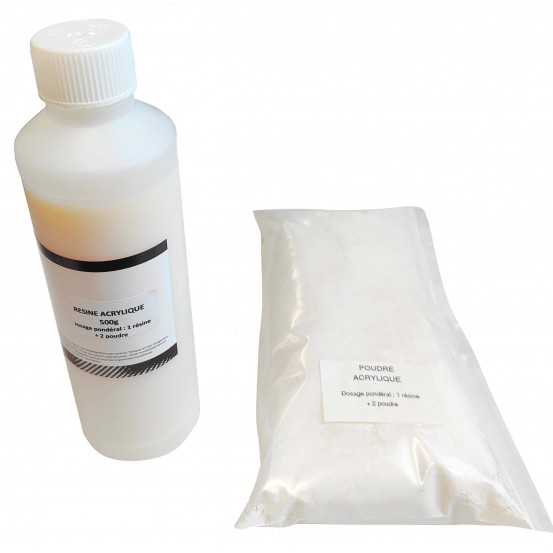
RÉSINE ACRYLIQUE
Résine bi-composants composée d'une poudre minérale à base de gypse (sulfate de calcium) et d'un polymère acrylique à base d’eau.
Non toxique, d’une mise en œuvre simple, respectueuse de l’environnement, la résine acrylique convient à de nombreuses applications.
Cette résine acrylique offre une bonne résistance mécanique et peut être utilisée pour mouler des pièces, en coulée, casting, dans des moules en silicone, ou stratification dans des moules composites, bois ou autre (suppose l’utilisation d’un agent démoulant). Elle peut également être pulvérisée et rotomoulée. Elle est très utilisée pour les décors de théâtre ou de cinéma, les parcs d'attraction, les loisirs créatifs etc.
Mise en œuvre :
- Le rapport de mélange pondéral est de 1 part de résine + 2 parts de poudre.
- Versez la poudre sur la résine et mélangez vigoureusement pendant au moins une minute. Le mélange doit être effectué très soigneusement, à l’aide d‘une balance précise, de préférence à l’aide d’un mélangeur à palette afin d’éviter les grumeaux.
-Pour une stratification tous types de tissus peuvent être utilisés, en revanche en ce qui concerne les mats de verre, seuls les ensimages poudre sont compatibles.
- Le temps de travail est d’environ 20-25 minutes et peut être prolongé par l'ajout du retardateur de prise, ou diminué à l’aide de l’accélérateur.
-Le temps de démoulage varie en fonction de l’humidité ambiante et de la température, l’humidité résiduelle de la résine devant s’évaporer pour obtenir un durcissement complet. Démoulez dès que la pièce est suffisamment résistante, le durcissement complet s’effectuera hors du moule.
-Selon les conditions, le démoulage peut intervenir en moyenne au bout d’une heure, le durcissement complet hors du moule pouvant prendre plusieurs jours en fonction de la taille de l’objet.
Adjuvants :
Pour optimiser l’utilisation de la résine, des additifs sont disponibles, qui peuvent prolonger ou raccourcir le temps de travail, ou épaissir le mélange.
-Retardateur de prise : maximum 0,5% de la partie résine
-Accélérateur de prise : maximum 1% du mélange résine+poudre
-Agent thixotrope (épaississant) : goutte à goutte jusqu’à obtention de la densité désirée (maximum 2% du mélange résine + poudre)
Caractéristiques techniques :
(Tests réalisés sur une éprouvette de verre E, à 20°C de température ambiante et 65% d’humidité relative).
Résistance au feu :
Répond aux normes Européennes de classification feu : B s1 d0
En accord EN 13501–1 : 2002
Vous aimerez aussi